钢铁是结构性、功能性材料,其消耗量约占金属总消耗量的95%,钢铁工业在世界文明史的进程中发挥了不可替代的作用。近几年,我国年消耗成品铁矿石12亿吨以上,由于我国铁矿石“贫、杂、细”的资源特征,国产铁矿石远不能满足钢铁工业的需求,对外依存度高达80%以上。
由于选矿技术和装备的限制,我国储量超过100亿吨的菱铁矿、褐铁矿和超细粒赤铁矿,只能低水平利用或根本不用,大量与磁(赤)铁矿共生的此类矿石则流失至尾矿库。开发高效利用难选铁矿石、综合回收流失至尾矿的铁资源的新技术和装备,解决极难选红铁矿分选技术难题,可有效拓展我国铁矿石资源储量、提高我国的资源利用率、有效缓解铁矿资源的供需矛盾。这对我国钢铁工业健康发展、保障国家经济安全,具有十分重要的战略意义。
菱铁矿、褐铁矿、微细粒赤铁矿和含铁废渣的高效利用是世界性难题,采用传统物理选矿组合方法只能得到铁品位40%~55%、回收率50%~60%的较低技术指标。实验已经证明“磁化焙烧-磁选”是处理该类资源最有效的方法,前期得到工业应用的磁化焙烧炉型只有竖炉和回转窑。竖炉焙烧由于透气性的要求,只能处理15~75mm的块矿,焙烧时间8h~10h。回转窑焙烧方法处理0~25mm的粉矿,焙烧时间60min~90min,我国自上世纪60年代开始研究,在陕西大西沟、新疆喀什等地得到大规模应用。沸腾炉(流态化)焙烧在国内外均有研究,但未见工业应用报道。这些焙烧方法都是处理粒度较大的铁矿石,与物理选矿方法比较,铁回收率得到一定幅度的提高,但存在焙烧时间长、热耗高、焙烧矿质量不均、铁回收率和设备作业率偏低等问题,严重制约了其工业应用。为此,中国工程院余永富院士提出了“闪速磁化焙烧”设想。
在余永富院士的引领下,2000年长沙矿冶研究院、武汉理工大学等单位强强联合,进行0~0.5mm粉状铁矿石流态化磁化焙烧技术研究,在数十秒内快速完成弱磁性铁矿的磁化焙烧,发明了闪速磁化焙烧成套技术。在国家科技支撑计划、国家重点基础研究发展(973)计划的支持下,闪速磁化焙烧成套技术开发历经基础理论研究、成套技术与装置研发、系统工程技术开发、工业试验和产业化,系统解决了铁矿物磁性快速转化、还原性气氛与温度耦合控制、矿粉循环预热、煤的流态化无焰燃烧、矿石低成本制粉、装备大型化等技术难题。在技术走向产业化的过程中,逐步优化和完善,形成了成熟、可靠的系统工程技术。从而开辟了菱铁矿、褐铁矿等难选弱磁性铁矿资源高质量、高资源利用率、低成本开发利用的新途径,引领着我国乃至世界难选铁矿石选矿技术的发展。
在项目研制的闪速磁化焙烧扩大连续试验装置中,对十余个典型难选矿样进行的闪速磁化焙烧-磁选试验结果见图1。与传统物理分选方法比较,闪速磁化焙烧提高铁精矿品位5~10个百分点、大幅提高回收率30个百分点以上!
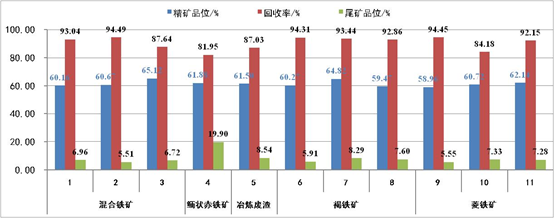
与竖炉、回转窑等焙烧方法比较,闪速磁化焙烧技术与装备具有显著的创新性:
1. 开发了铁矿流态化磁化焙烧技术,固气两相接触面积提高3000倍以上,反应速度提高100倍以上,实现了弱磁性铁矿物快速、均匀的磁性转化 。
2. 新研制了循环预热、尾气二次燃烧的流态化磁化焙烧装备。
3. 开发了流态化无焰燃煤新装置,可用普通燃煤为焙烧系统同时提供热源和还原介质,有利于降低焙烧能耗和成本,大大拓宽了工艺技术的适用地域。
4. 原矿石采用干式磨矿工艺,在制粉的同时利用焙烧尾气余热循环干燥矿粉,解决了低成本制粉难题。
5. 集成创新多种综合节能和环保技术,形成产业化新技术,显著降低NOX排放,实现了无废水排放和尾矿综合利用,全过程满足了清洁生产要求。